AUTOMATION OF PUMP CAPS TIGHTENING LINE FOR CONSUMER GOODS INDUSTRY
The pump capping line automation solution implemented by ETEK not only helps optimize production efficiency but also ensures consistent product quality, saves operating costs and improves quality control capabilities thanks to the ability to detect errors right in the process.
CHALLENGES FOR BUSINESSES
A leading company in the personal care products sector in Vietnam is facing the problem of increasing productivity while maintaining quality and reducing production costs, in the context of strong consumer demand.
In particular, the process of tightening the pump cap for product lines such as shampoo, shower gel, hand soap, dishwashing liquid, etc. is a major bottleneck. Manual implementation causes limitations in speed, uneven tightening force leading to product leakage, affecting brand image and customer experience. In addition, ineffective inspection and classification of defective products also increases production costs and the rate of defective products.
In addition, businesses also have to handle many product lines with diverse types of bottles and pump heads, making the automation process encounter many obstacles in terms of flexibility and system synchronization.
TECHNICAL REQUIREMENTS
- The line needs to process 30 product codes (SKUs), corresponding to 10 different types of pump heads.
- Maximum speed: 150 products/minute, ensuring to meet the pace of the entire factory.
- Flexible format conversion capability, quick conversion when changing products.
- Tightening must be precise and stable to avoid misalignment or pump mismatch.
- Integrate camera inspection system and automatically remove defective products.
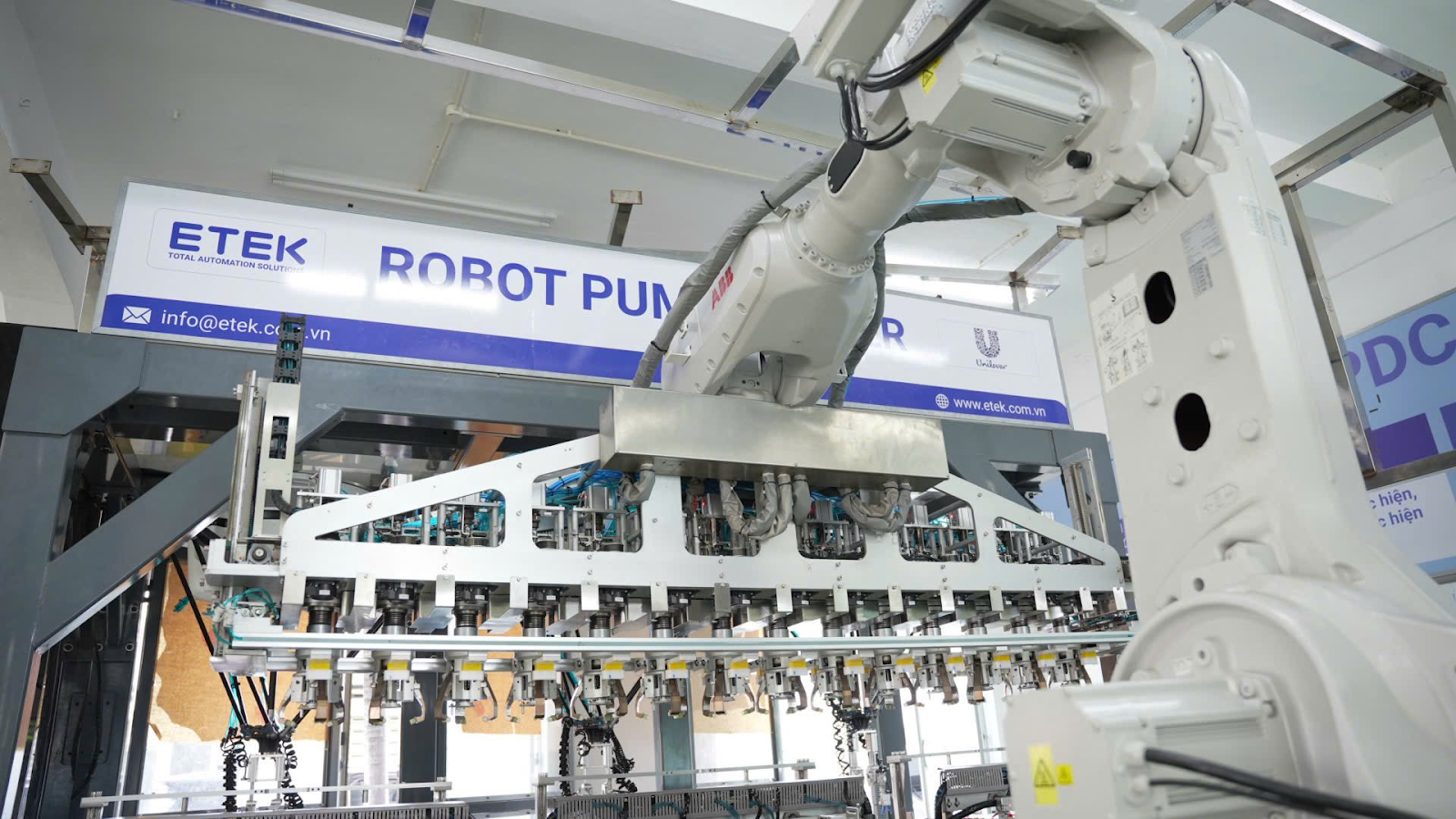
ETEK’S COMPREHENSIVE AUTOMATION SOLUTIONS
Based on the specific requirements of customers, ETEK has designed and implemented an automated pump capping line system with a capacity of up to 150 bottles/minute. The system integrates many modern technologies:
- Automatic pump feeding
hopper The pump head is fed through a vibrating hopper, helping to arrange the material in the right direction and stabilize it before entering the line. - Pump head return conveyor
Defective or unusable pump heads are returned for reprocessing, reducing waste. - Navigation conveyor
Integrates sensors and counters to control the position of each bottle, helping to synchronize the next steps. - Camera input inspection system
Industrial cameras check bottle condition and remove defective products before entering the pump installation stage. - Pump head picking robot
The robot is programmed to recognize and pick up the correct pump type for each SKU, ensuring high accuracy. - Transfer buffer and pump return system
The pump head is held at the transfer point to synchronize with the tightening robot. Any pumps that do not match are returned to the supply system. - Automatic pump switch
Puts the pump head in the correct position at the bottle mouth, facilitating the tightening process. - Specialized pump cap tightening robot
Customizes tightening force for each pump type, helping to ensure precise and uniform tightening. - Post-tightening inspection by camera
The camera performs a final check of the cap position and tightness. Unqualified bottles are automatically removed from the line.
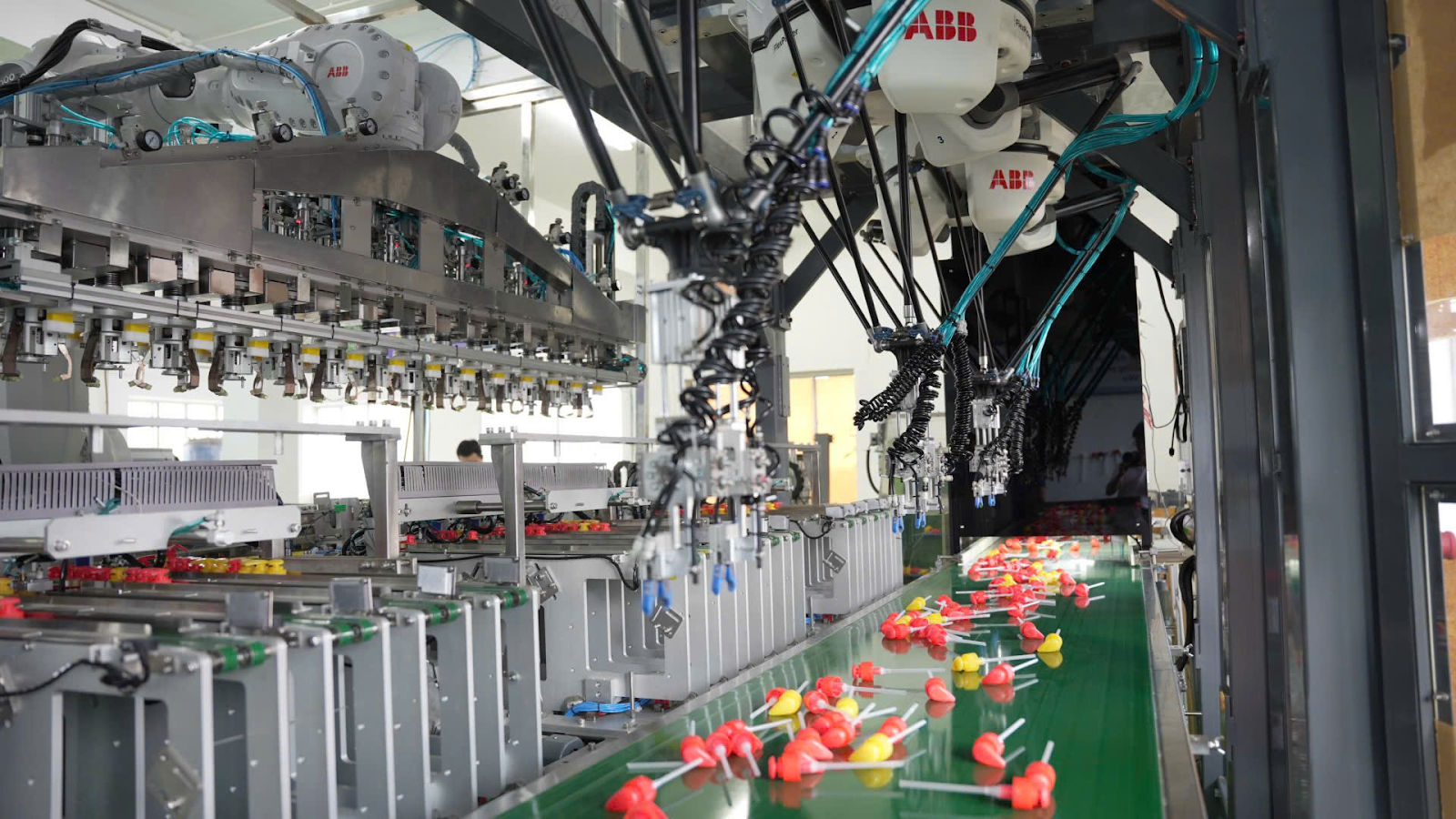
RESULTS ACHIEVED
Putting the automated production line into operation has brought many obvious benefits:
- Production speed increased significantly, far surpassing traditional manual methods.
- The quality of the cap tightening is guaranteed to be consistent, eliminating leakage or loose cap.
- Defective product rates are dramatically reduced thanks to real-time automated inspection and rejection systems.
- Reduce final inspection costs while saving manpower thanks to the almost completely automated process.