AUTOMATIC DATE PRINTING AND QUALITY CHECKING SOLUTION FOR SNACK PRODUCTION LINE
ETEK successfully deployed an automatic quality control and production date printing system for snack production lines.
Problems customers are facing
During the production process, businesses face many serious obstacles such as:
- The can contains no product inside.
- The can mouth is deformed during the forming or packaging stage.
- Production date and expiry date are printed incorrectly or missing information.
- Lack of automated systems to eliminate defective products at high speed and high accuracy.
With the requirement to ensure output quality and integrate with the traceability system, customers need a comprehensive automated testing solution that operates continuously and meets high production speeds.
Integrated solutions from ETEK
ETEK has designed and implemented an automatic quality control system including: date code printer, sensor system, industrial camera, image processing software and pneumatic defective product removal cluster. The system helps to quickly detect and remove substandard products directly on the production line.
Process of checking can shape and product inside:
- Product Transport: Snack cans move continuously on conveyor belts to the inspection area.
- Presence Detection: The first sensor detects the can and activates the height checker to determine if there is product inside.
- Shape Check: A second sensor triggers a camera to take a picture of the can’s mouth to check for deformations.
- Data processing: Image processing software collects data from sensors and cameras to classify products as passing (OK) or failing (NG).
- Automatic Reject: Cans identified as NG are removed from the line by pneumatic assembly, ensuring uninterrupted product flow.
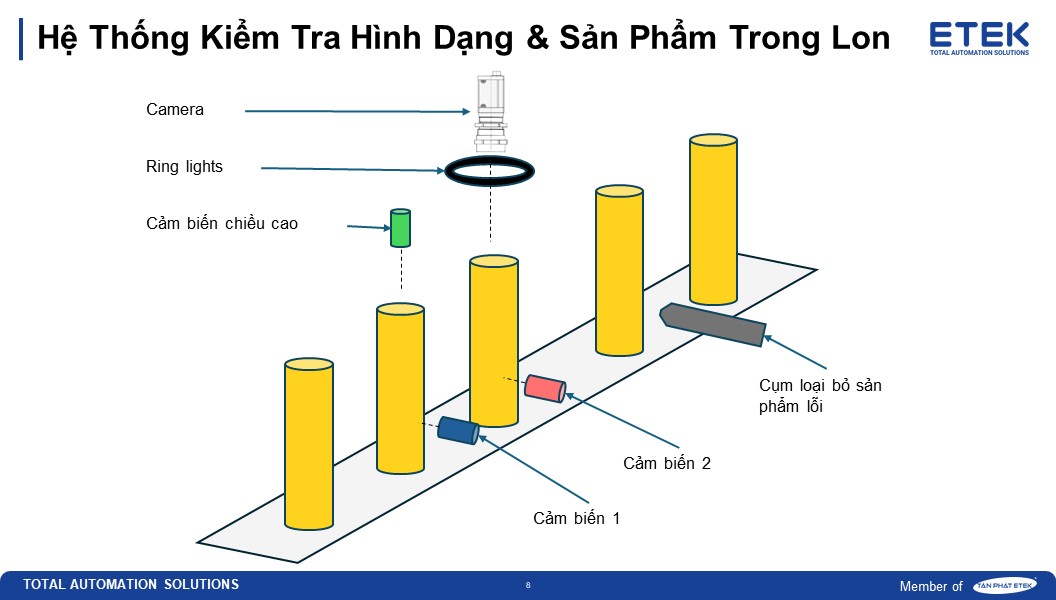
Print content checking process:
- Printing product information: When the can reaches the printing position, the Markem-Imaje printer prints the production date and expiration date.
- Camera Trigger: The printer simultaneously sends a signal to the camera to initiate the inspection process.
- Image analysis: The camera captures the printed content and transmits the image to the processing program for optical character recognition (OCR).
- Comparison and Evaluation: The readings will be compared with the original printed data to determine whether the can passes or fails.
- Defective product rejection: Cans with incorrect printed content will be automatically rejected by pneumatic assembly.

Results achieved
The application of ETEK’s automatic testing system has brought practical benefits:
- High inspection speed: Achieve 250 cans/min performance , suitable for production line speed.
- Absolute accuracy: 100% accurate identification of defective products such as empty cans, distorted mouths or misprinted content.
- Fully automated: Completely eliminate manual testing, minimizing human error.
- Reduce operating costs: Optimize personnel costs while improving work efficiency.
- Stable quality: Products brought to market have optimal quality, enhancing brand reputation.
Long-term companionship with customers
ETEK is committed to always being a reliable partner throughout the system implementation and operation process. With a team of highly specialized engineers, we provide 24/7 technical support services to ensure the system always operates smoothly and effectively. We believe that dedicated and timely support is a solid foundation for customers to confidently expand production and develop sustainably.