AUTOMATIC BAG-PACKING LINE WITH CAPACITY OF 1200 BAGS/HOUR
ETEK has successfully developed a fully automated bagging line , capable of producing up to 1,200 bags per hour. This automated system integrates many advanced equipment and technologies, from automatic conveying systems, bag printers, automatic weighing and information checking systems, to defective bag detection and rejection features.
Challenges from the customer side
- Production capacity: Previously, the factory operated entirely by manual labor, resulting in low production efficiency and not being able to meet the increasing orders. Hiring more workers means higher costs and is not an optimal solution in the current industrialization context.
- Product Accuracy: Manual operation in barcoding and checking often causes errors, affecting product quality.
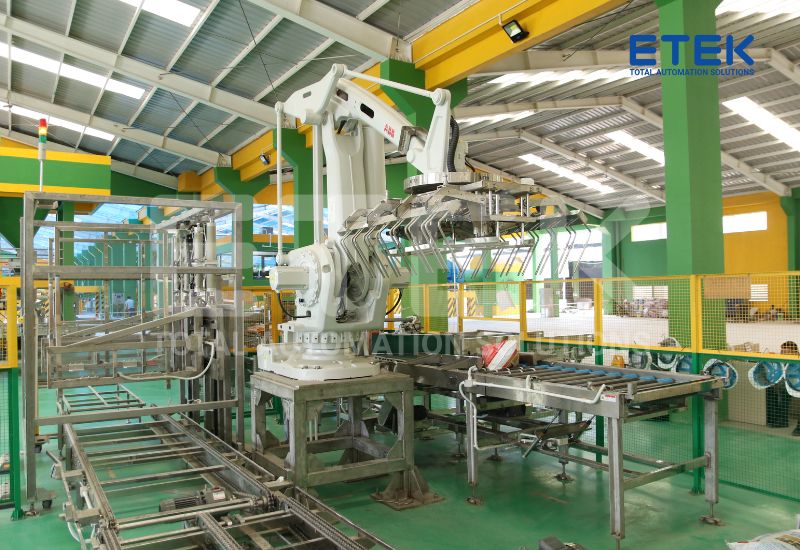
Requirements
- Automation: Customers want a complete automated production line, from bagging to palletizing, integrating weighing, printing product information and automatic error reporting.
- Productivity and time: In a fiercely competitive environment, factories need to increase output while shortening production time, ensuring flexibility in adjusting output according to market demand without reducing quality or increasing costs.
- Product quality: Products must ensure correct quantity and information, minimizing errors arising during manual production.
- Operational safety: The line must ensure absolute safety during operation.
- Factory digitalization: Businesses want to digitally transform to improve competitiveness and maximize the potential of technology in production.
ETEK’s solution
Upon receiving the request, ETEK quickly implemented a comprehensive automation process, completing the project in just over 4 months. The implementation process included consulting, needs analysis, technical design, construction planning, installation and handover.
ETEK’s automatic bagging line is designed to meet the packaging needs of 25kg and 50kg bags , while integrating modern technology to optimize production efficiency and flexibility.
The automatic system includes:
- PVC conveyor belt guides bags, transports bags from the filling area to the packaging stage
- Bag flip conveyor, transferring bags from standing to lying state
- Bag conveyor, evenly distributes product inside the bag
- Conveyor belt presses bag, flattens bag surface before printing information
- Bag weighing conveyor, automatic bag weight checking, ensuring accuracy
- Production information printer, automatically prints serial number, unique QR code for each bag, and warns when camera has problem
- Conveyor belt removes defective products
- Automatic palletizing robot conveyor
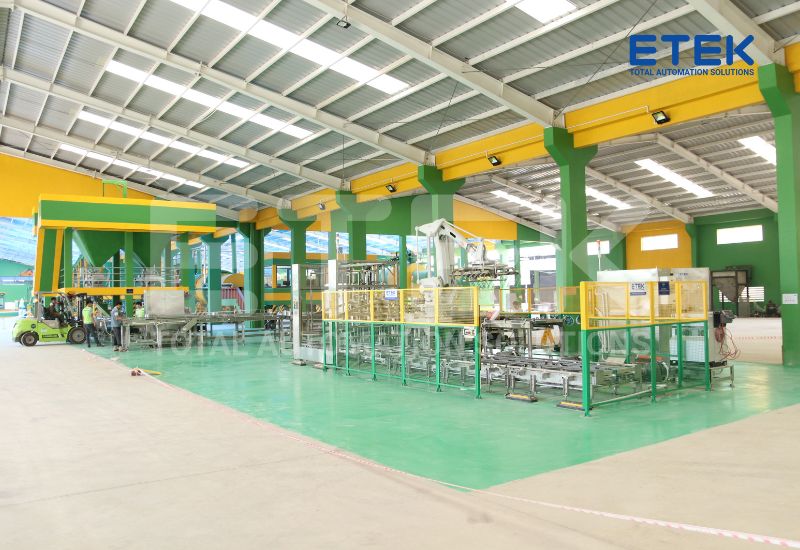
Results achieved
- Productivity increased by 150%
- Reduce production costs by 20%
- Product defect rate below 5%
- Achieve more than 50% factory digitalization
- Ensure absolute safety in operation
Thanks to this solution, ETEK has helped customers optimize production processes, improve productivity and product quality, and move closer to the goal of digitizing factories and adapting to the trend of Industry 4.0.